1
Suspension & Steering / Bumpsteer and Roll Centre Correction - A DIY Walkthrough
This post is fairly in depth and fairly nerdy… if that tickles your pickle stay tuned.
I chose to start with the Noath Engineering Roll centre correction and track rod flip kit. A lot of the off the shelf ones I don’t like the look of and I’ve heard numerous stories of them failing. The main reason for this kit was it was tried and tested on Nige’s golf, and they use really high quality materials.
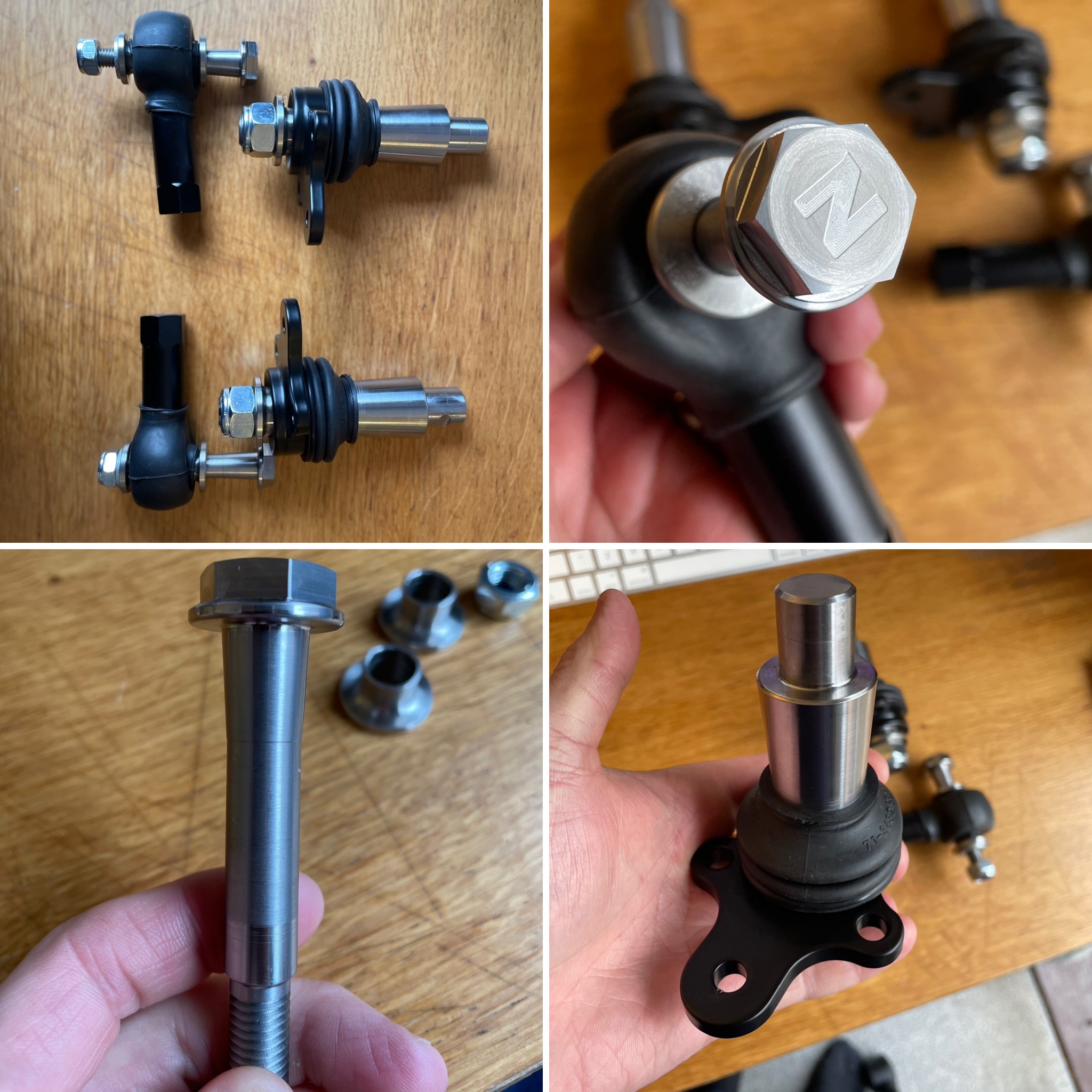
If you look at the angle of the wishbone it gives you an idea of the roll centre, before and after the kit.
OEM at ride height
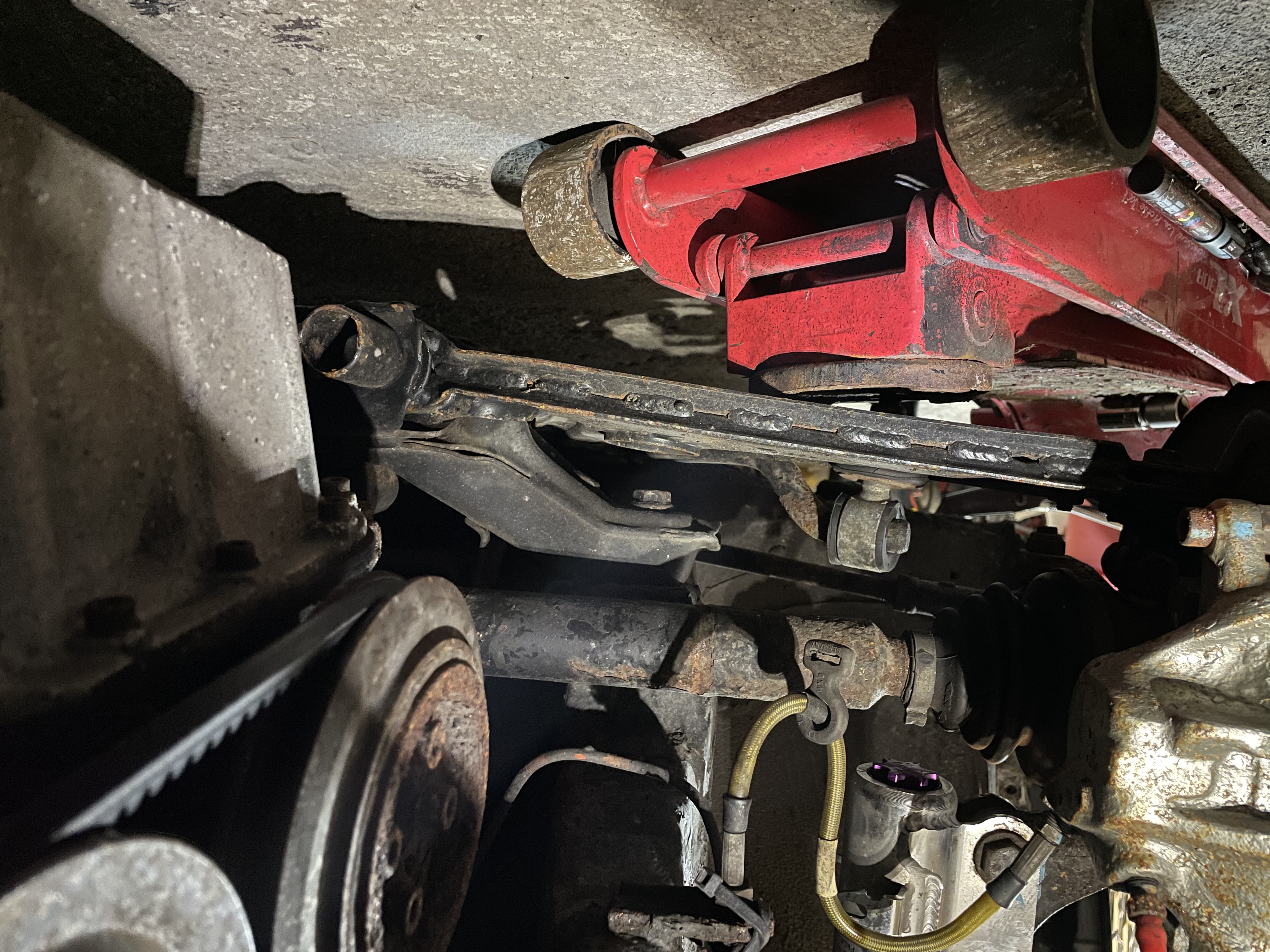
Noath Kit at same ride height
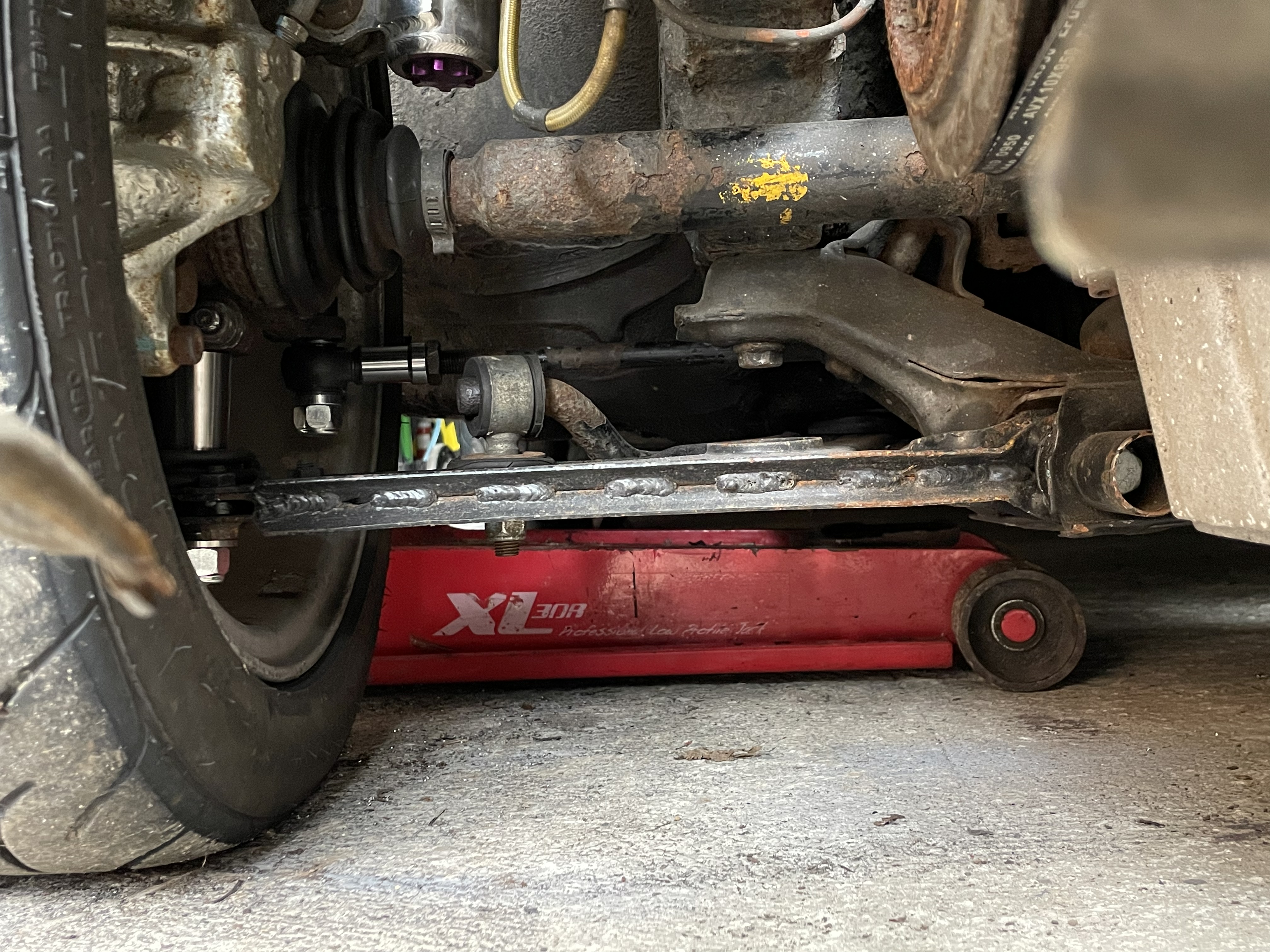
With roll centre you are limited by the size of the pins you can use in the BBJ, for interference with the wheel, especially on 15’s.
Now onto the track rod flip kit, I was thinking about fitting the kit and leaving it at that, but curiosity got the better of me and I wanted to work out exactly what the factory bumpsteer was, in comparison to the kit.
At this point I want to just reference Nige’s website for those who haven’t seen it, a lot of what I’ll be going through here, he has covered. www.pinderwagen.com
So, bump steer. What is it? and how do you measure it?
Bump steer to put simply, is unwanted toe change through a cars suspension travel. The changes can be pretty crazy, and this can cause unpredictability in handling – especially on track, where you will naturally use more of the suspension travel due to the forces.
Bumpsteer is effected by the arc created by the lower ball joint mounting point and the track rod mounting point, and their relationship to each other. – its almost like a push and pull effect.
How do you measure it? There’s a few ways, you could take it to a specialist, who will no doubt charge you an arm and a leg. There’s a Longacre gauge, which are upwards of £600. Which again isn’t feasible for us ordinary folk. And where is the fun in not learning along the way!?
Taking inspiration from the PinderWagen, I used 2 sheets of flat wood. I bought these from B&Q for £10 – much more respectable!
Before you do anything it’s important to take some initial measurement. With the front bumper and front wing removed, it gives great access to the suspension.
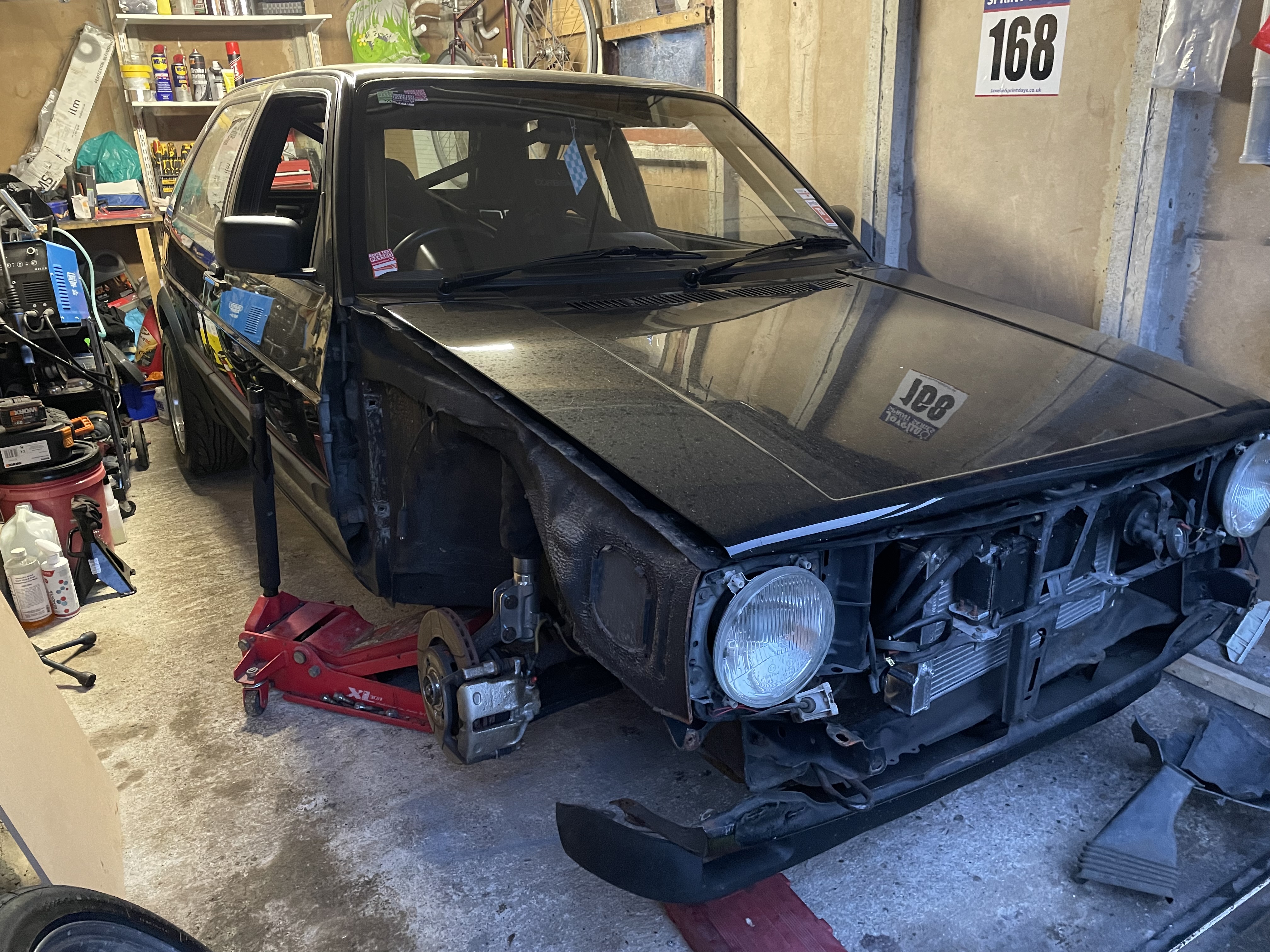
This is how I measure ride height, using a bolt in the hub and a block of wood on top of the inner wing. It’s also a good idea to measure the front sill to floor height at this point.
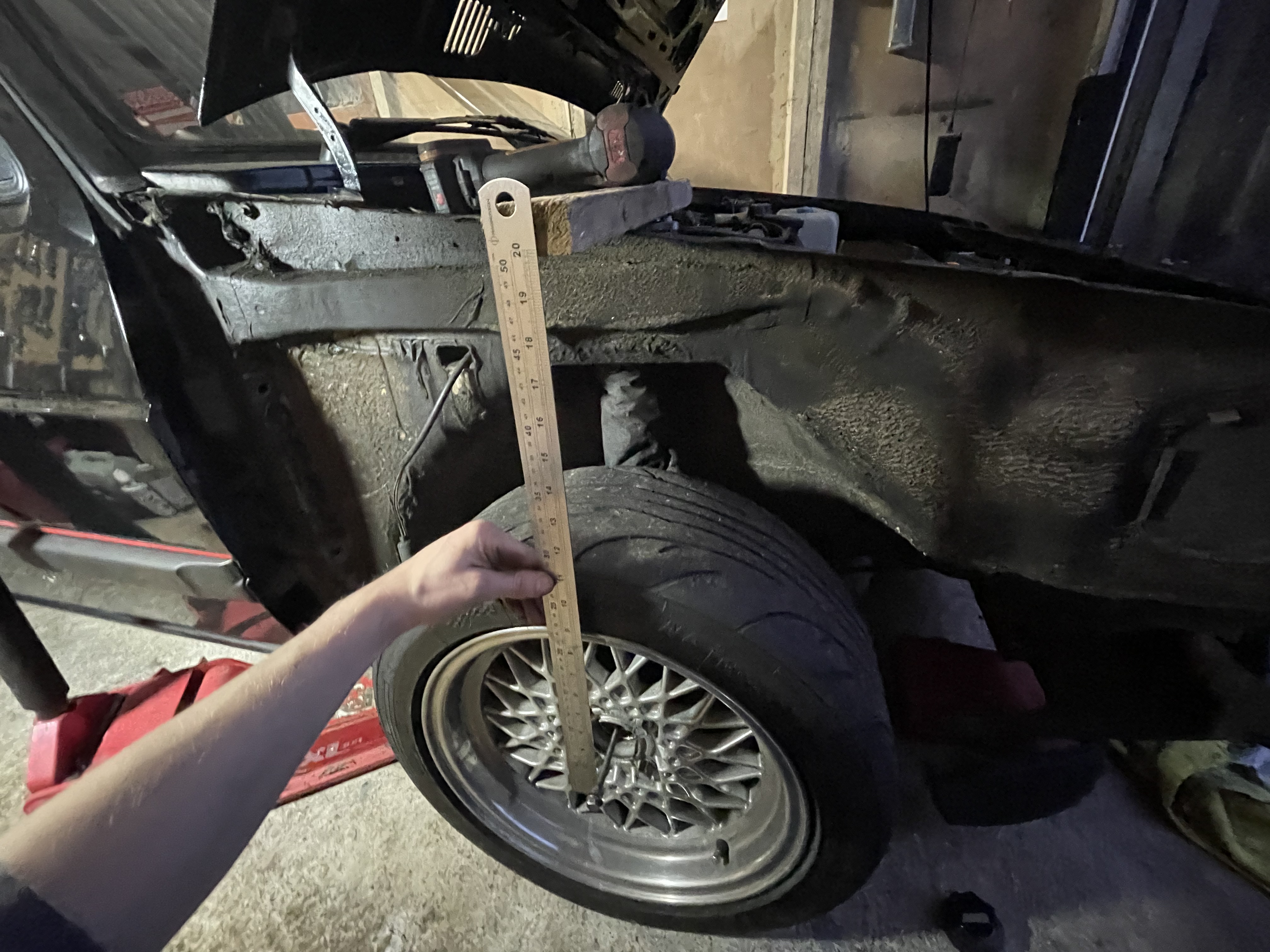
Next up you need to remove the front spring, this makes life a lot easier when jacking the suspension up and down.
Next up is to drill out the bolt pattern so it can be mounted to the hub.
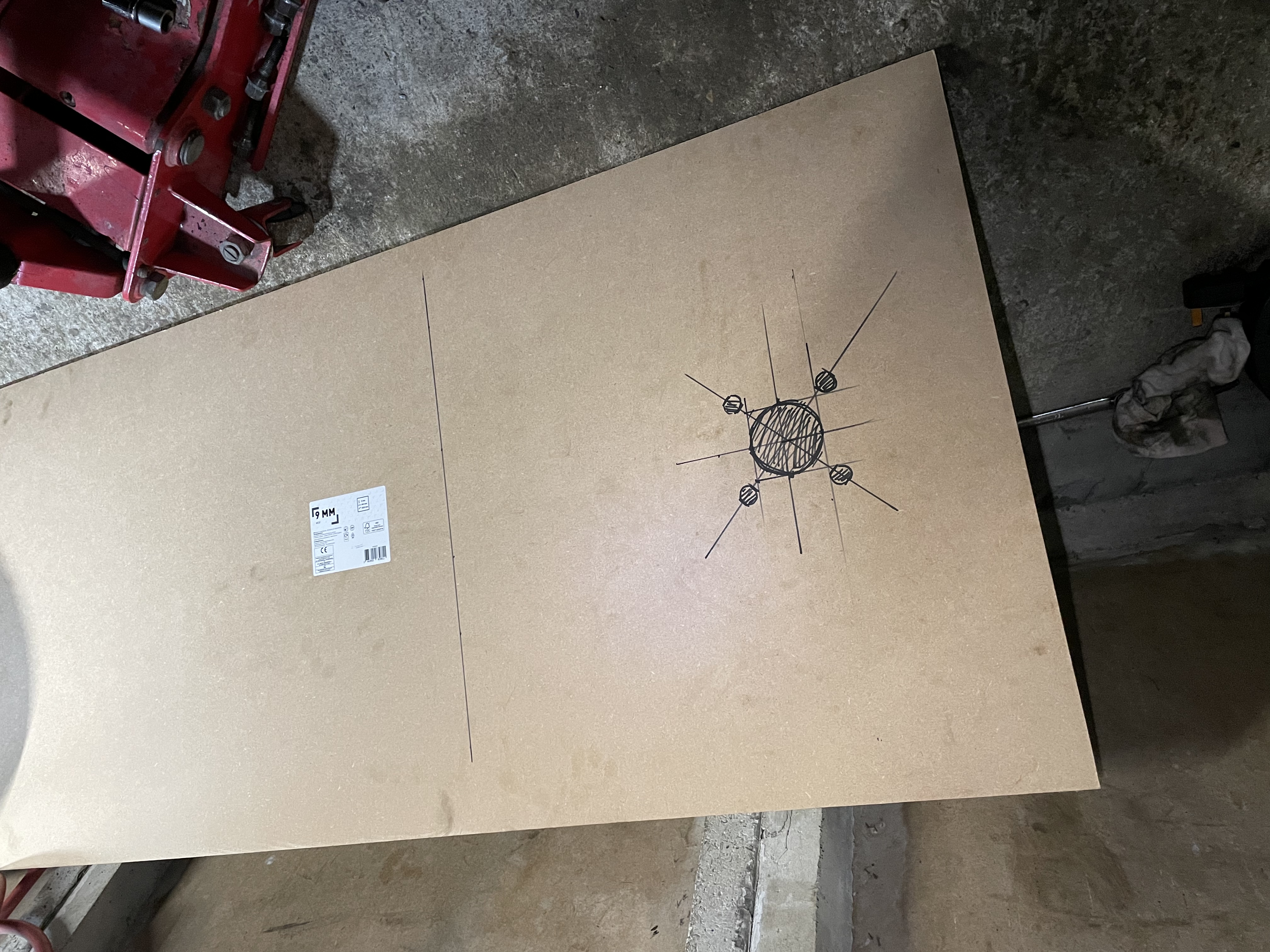
The wood was cut into 2 pieces, one will be bolted to the hub, the other will pivot off the floor, and the distance between the leading edge, throughout the suspension travel is where we will measure the bumpsteer.
There’s a few ways to measure it, you can use a steel ruler – time consuming and has ability for inaccuracies. Vernier calipers are another option, much more accurate but again a bit of a faff, measuring and remeasuring.
I chose to go for a dial gauge, they are fantastic, measuring 1mm through one full rotation of the dial, they are also very inexpensive, this was £8 on amazon.
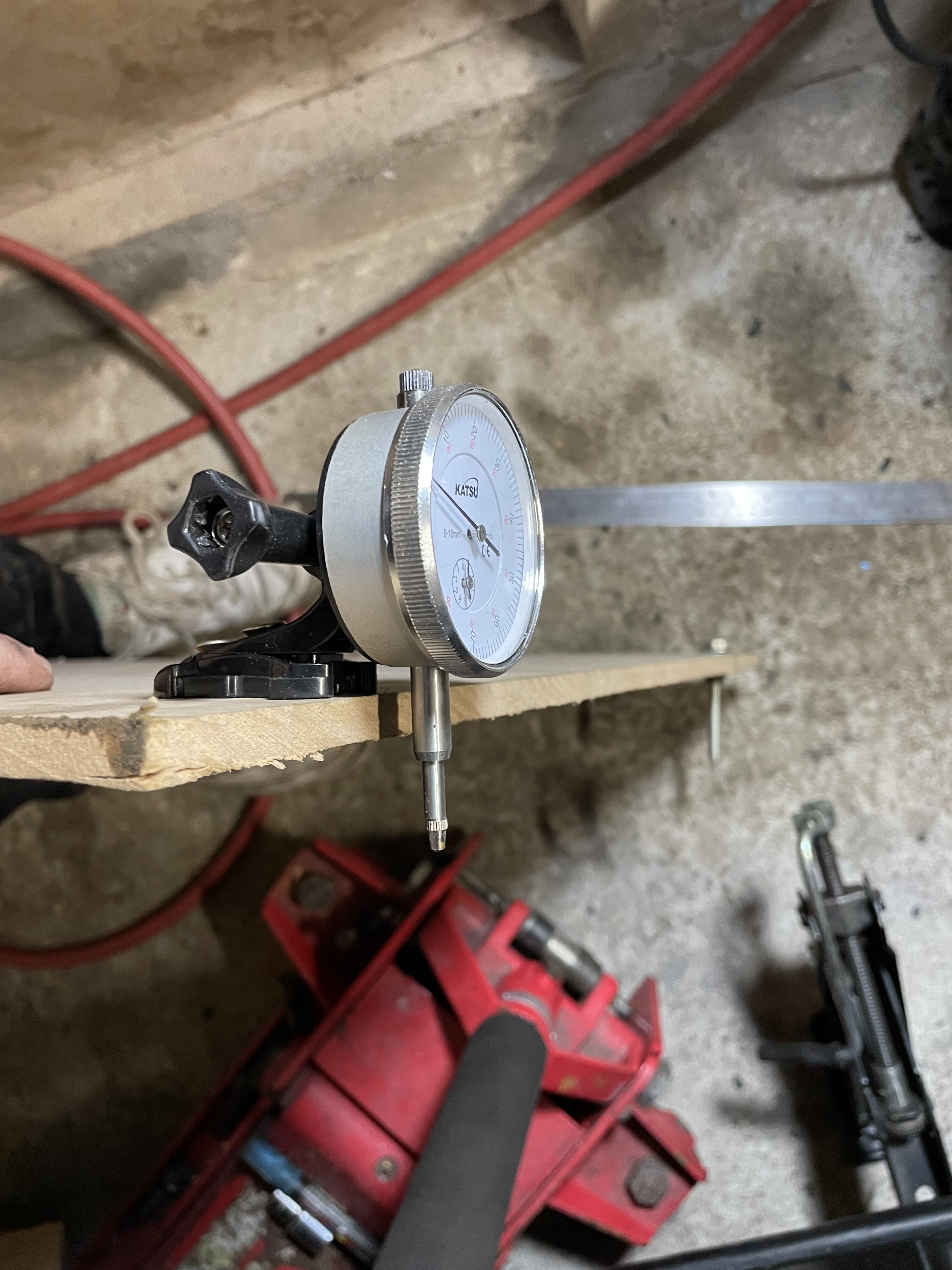
The gauge needs mounting to the wood, I used an old GoPro mount – this worked out really well.
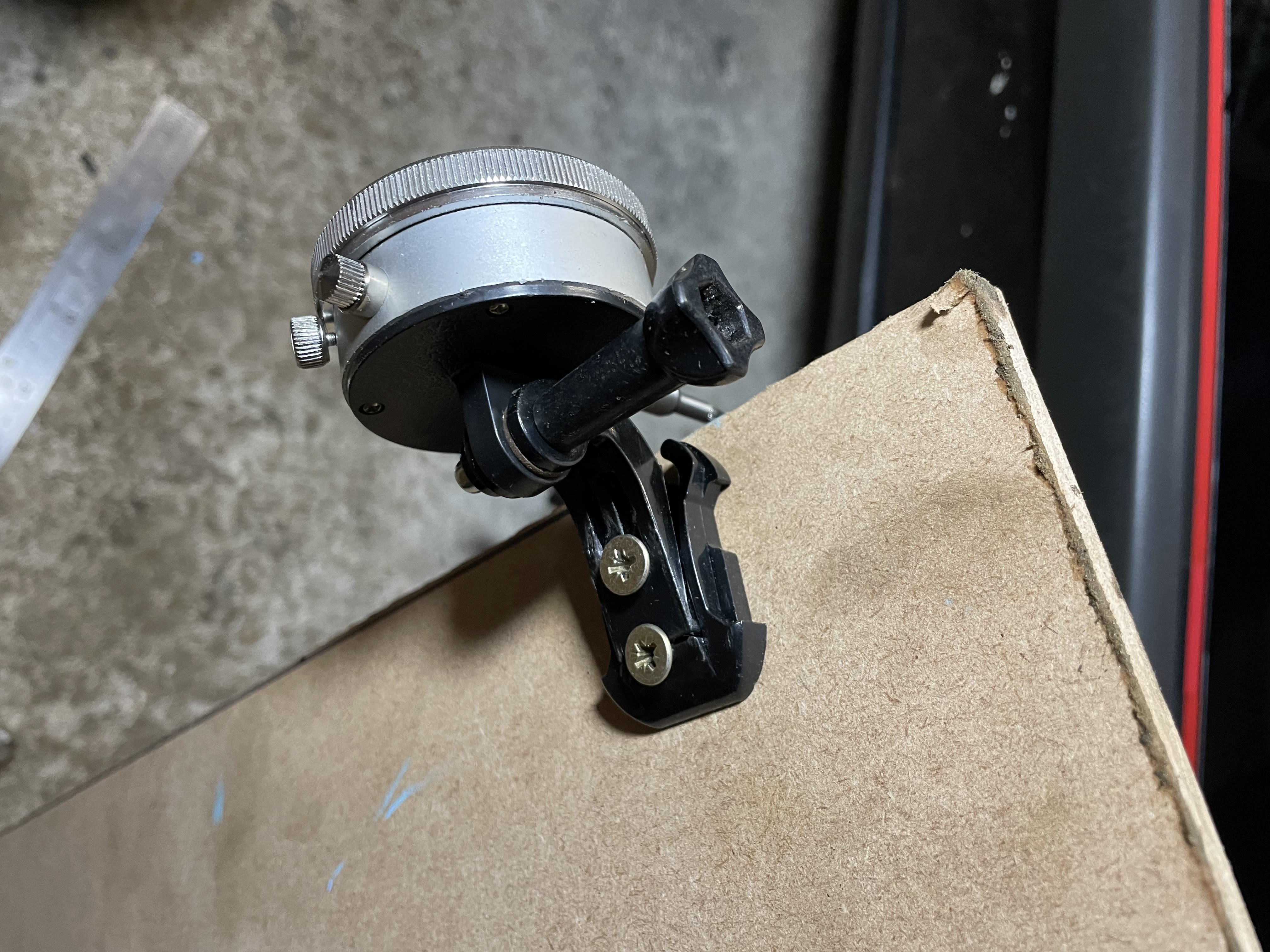
on the other side of the wood, mirror the length of the gauge with a bolt. This will remain constant and make any measurement visible on the gauge.
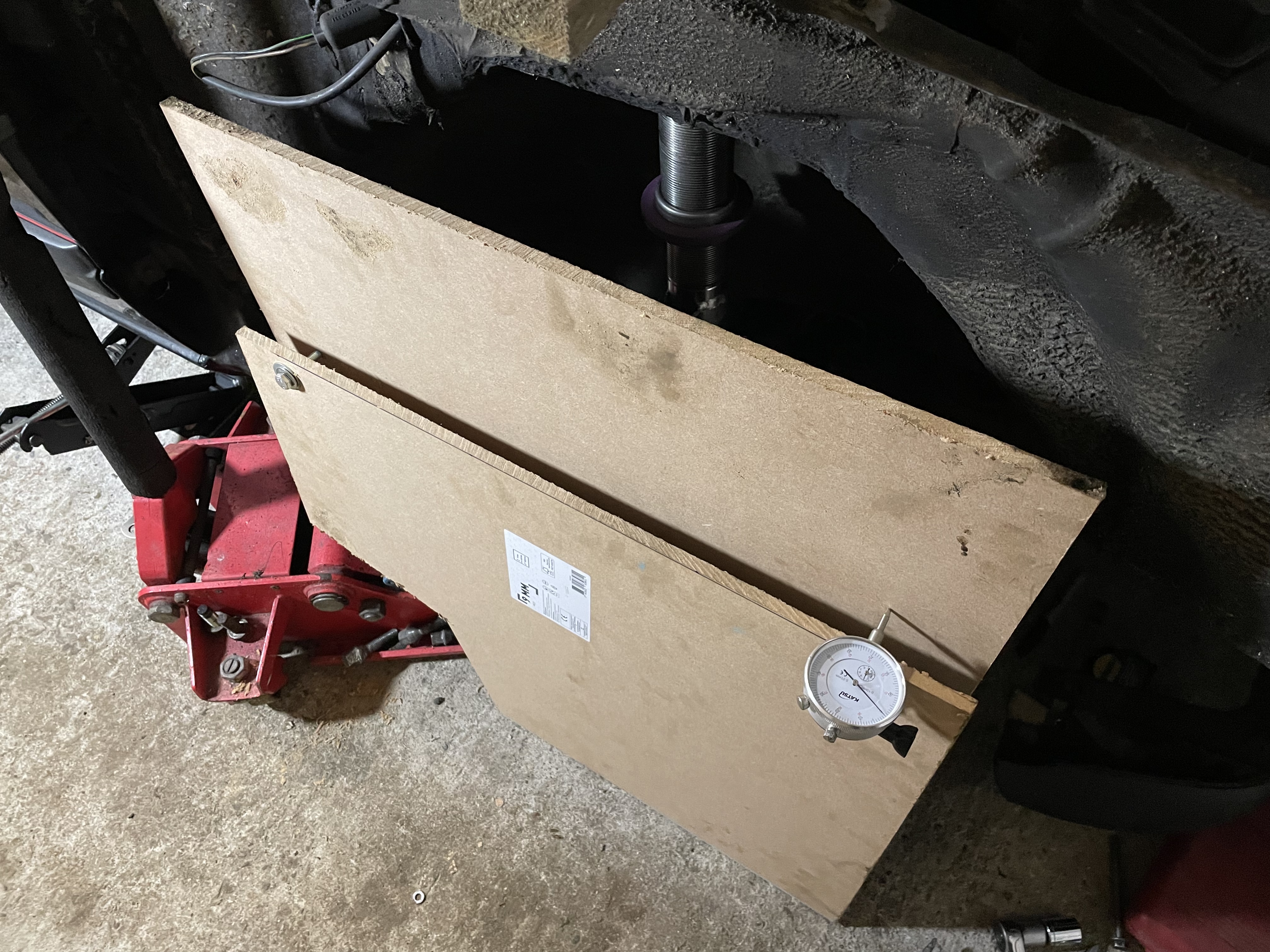
With everything ready to go, and the front wheel off, I lowered the car back down on the jack so it was the same height as the sill to floor height we measure previously. I don’t have 2 jacks and axles stands are too high, so I used the standard scissor jack to keep the height of the car consistent. My main jack I used to raise and lower the suspension.
The standard set up was then measured.
The best way I found to measure this accurately, was to jack the suspension up to ride height. The dial gauge was then zeroed. I then jacked the suspension up to full compression, released the jack slowly and filmed the dial gauge on my phone.
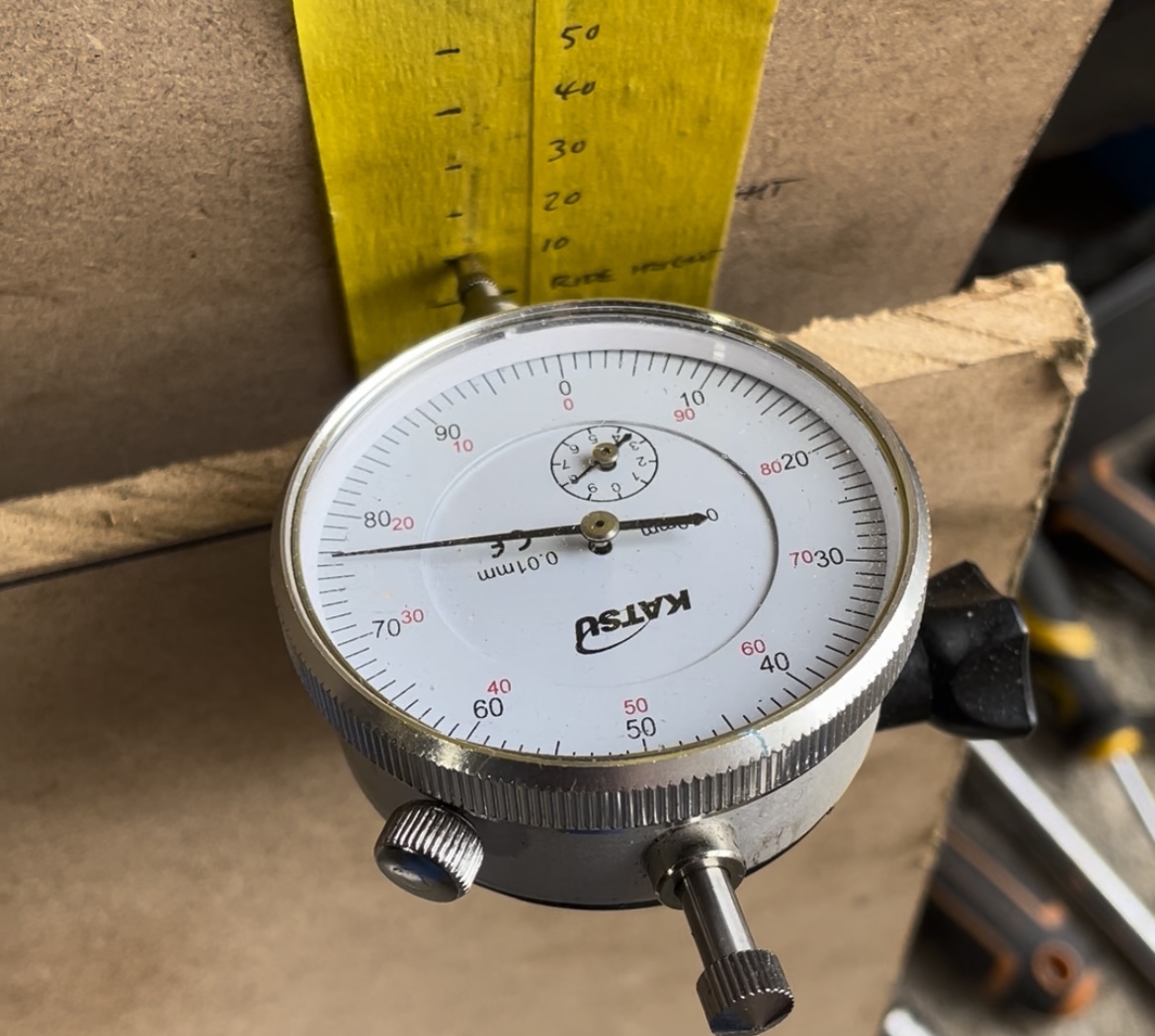
With the results filmed on my phone, I could sit inside and plot everything on a graph.
The straighter the line, the closer it is to zero bump steer.
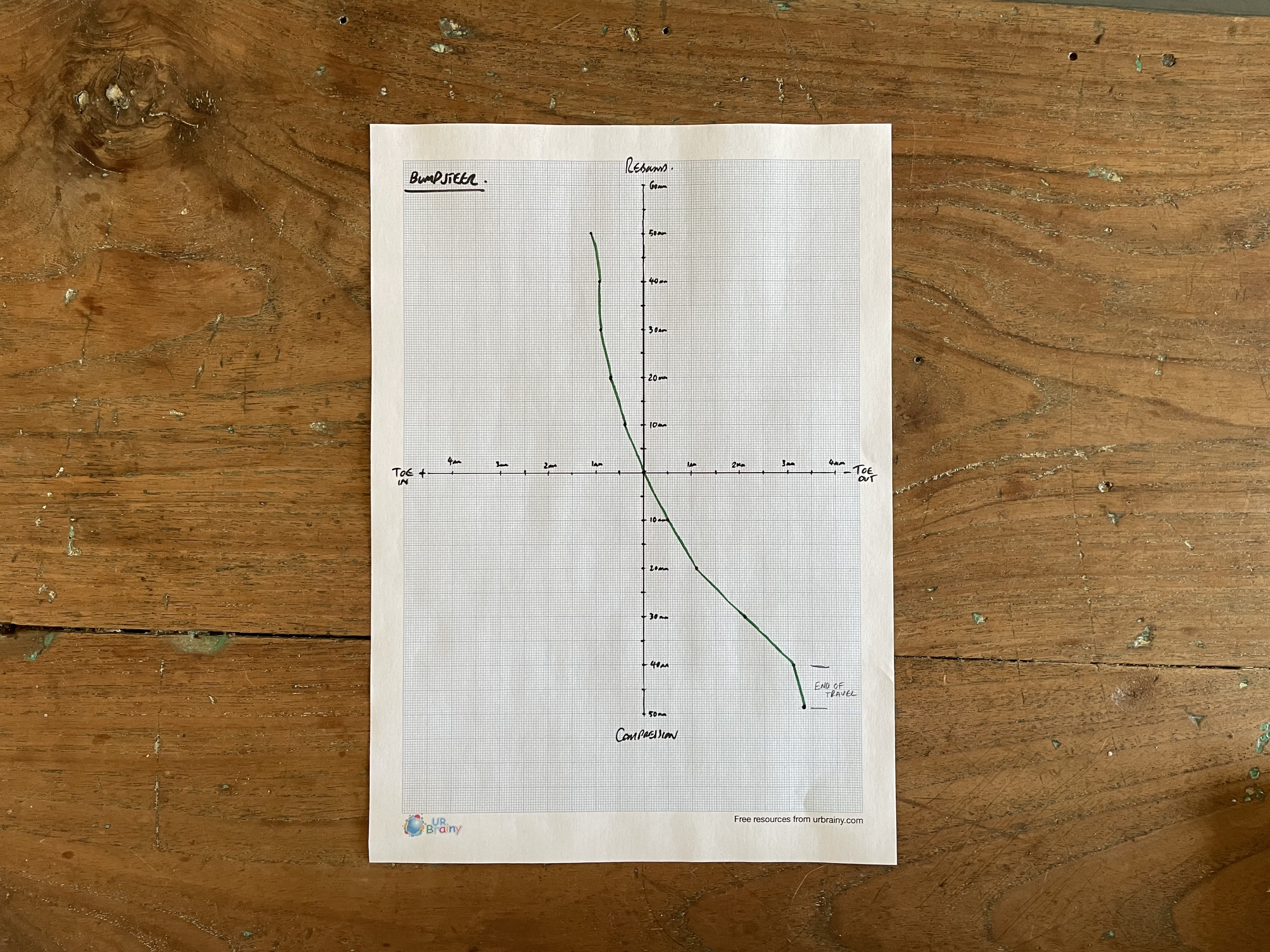
To explain the above:
X axis – Shows toe change in 1mm increments, toe in to the left, toe out to the right. (each small square on the graph is 0.05mm)
Y axis – Show suspension travel in 10mm increments, from full extension, through ride height to full compression (each small square is 0.5mm in travel)
The suspension was jacked up and every 10mm a dot was plotted on the graph, with a line of best fit to see it visually.
What we can see in this standard set up is we gain toe in as the suspension extends from ride height and gain toe out under compression.
In driving terms, toe out gain under compression isn’t necessarily terrible, certainly more favourable than toe in, which I think is why the car felt pretty good anyway. – But we are still seeing over 3mm of toe out at 40mm compression, which is significant.
So how does the Noath Kit compare?
Well, as we mentioned earlier, the relationship between the LBJ and the track rod is what effects bumpsteer, so if you were to just fit the extended ball joints and keep the track rod as standard the bumpsteer would be horrendous, quite literally unmeasurable!
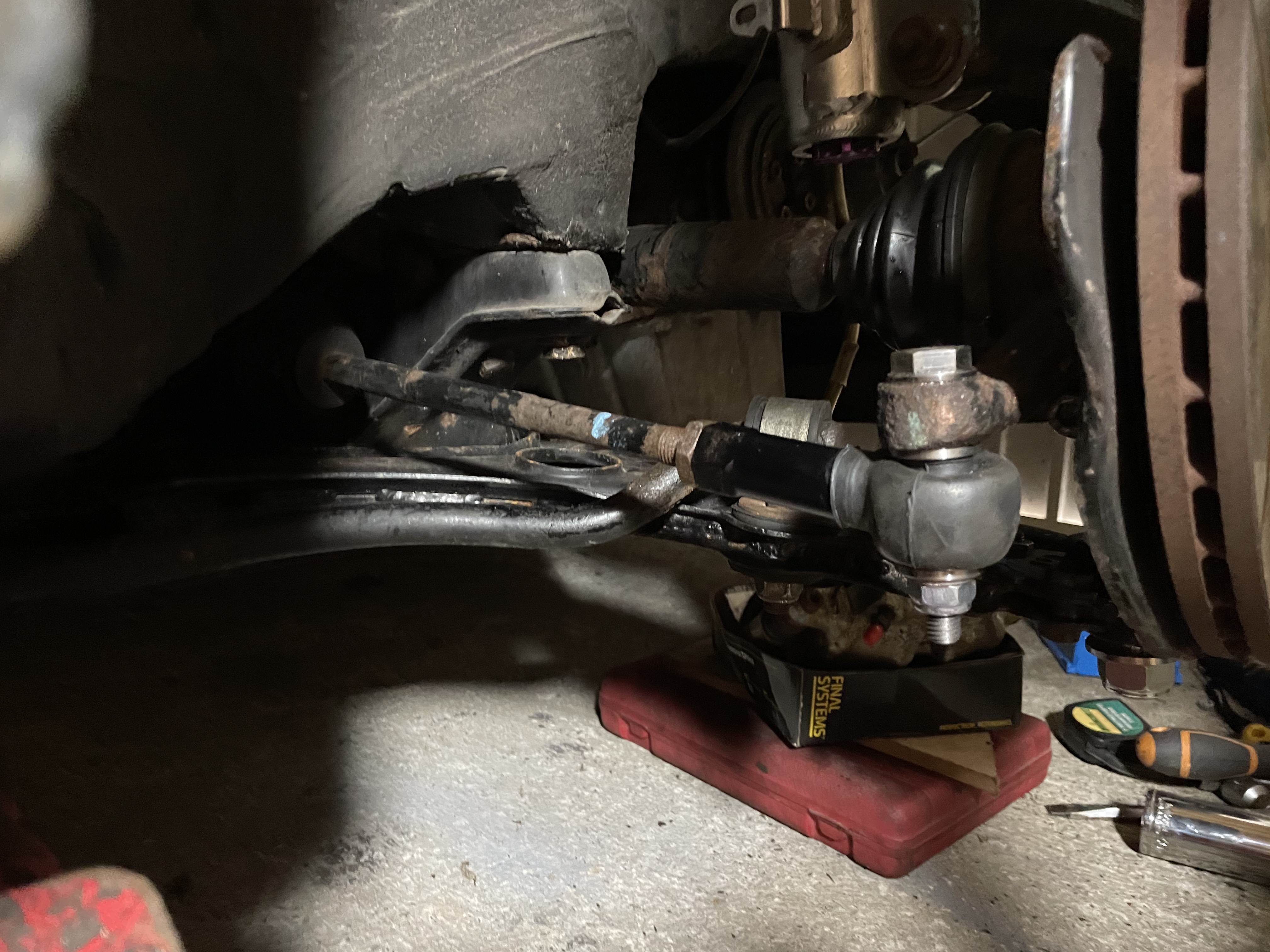
I’ll also point out at this point that bumpsteer is bespoke to each car, there’s no one size fits all. Noath doesn’t sell this as a ‘bumpsteer kit” the idea of flipping the track rod is to get the bumpsteer back towards oem, as best they can for a bolt on kit.
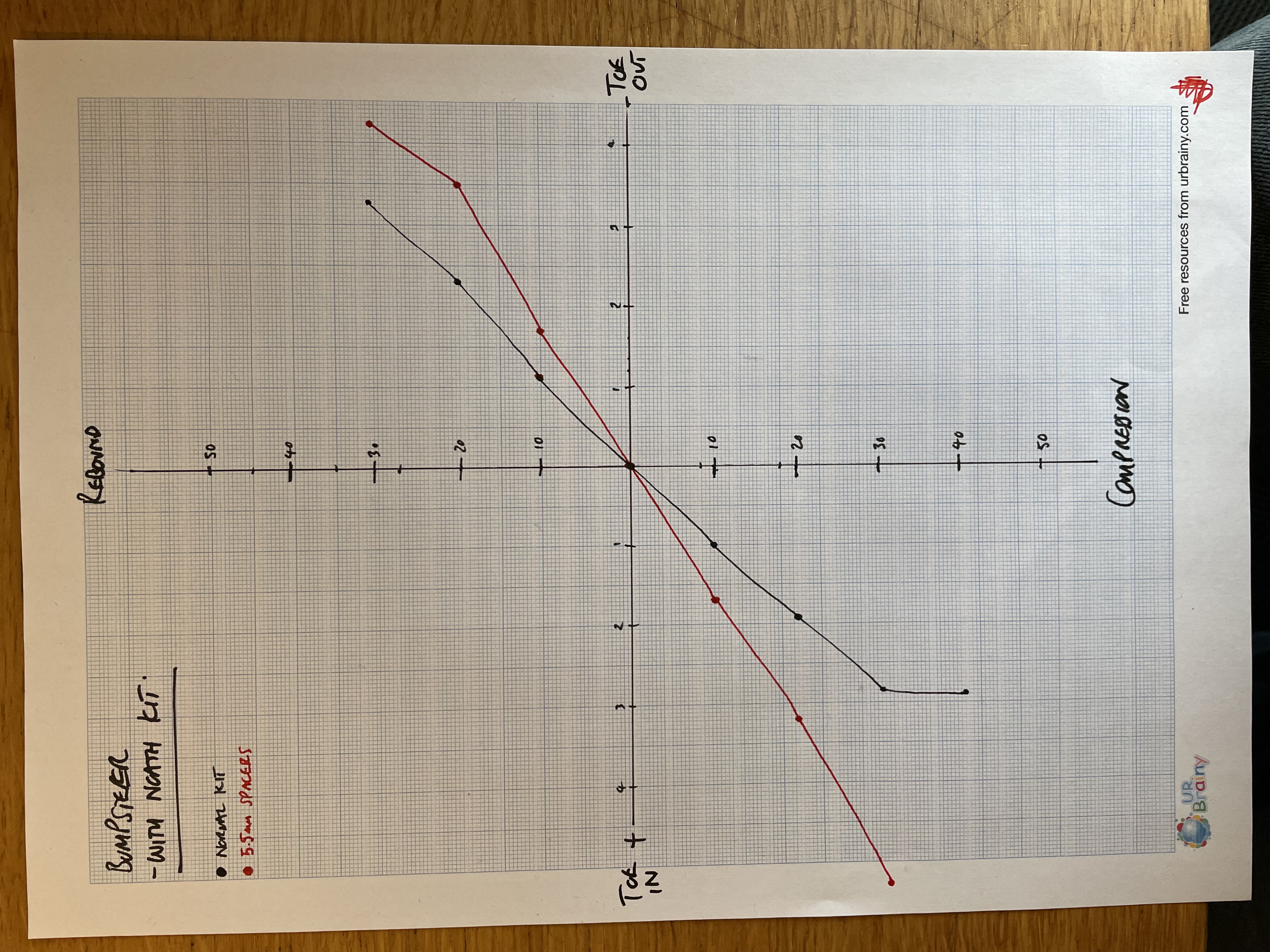
This graph shows the Noath kit, as it is, as you can see its actually worse for bumpsteer than the oem set up. So although we have corrected the roll centre, that has now had a direct effect on bumpsteer and made it worse.
The red line on the graph shows the track rod end lowered 5.5mm using washers, this was to see which way I need to move the track rod. As you can see the redline is worse still.
With that data collected I had to work out a way to move the track rod up. I could cut down the misalignment spacers Noath provided, but there was a casting on the track rods which would need to be ground down.
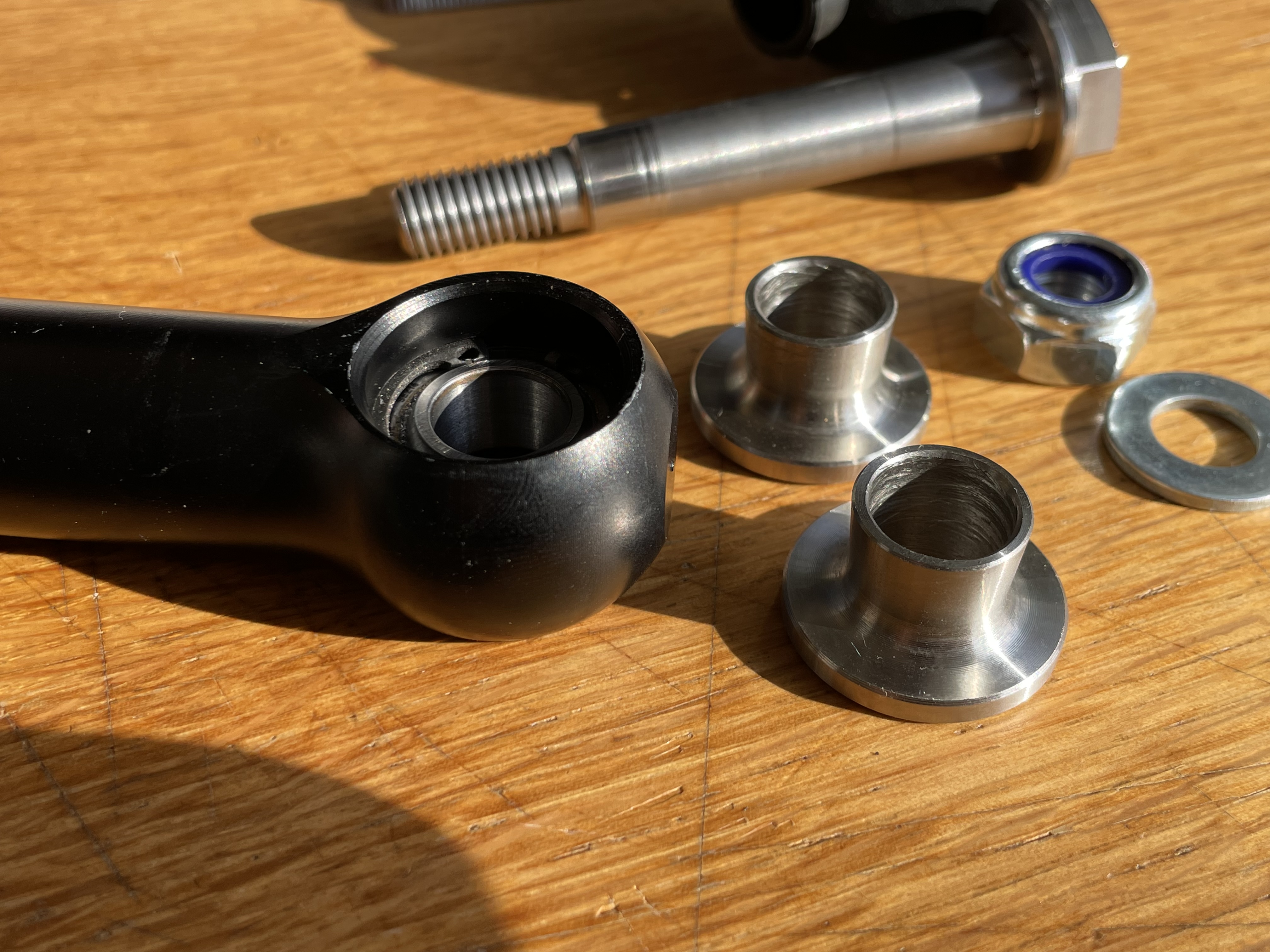
Going over the graphs again, I’d worked out I’d need more than just a trim of the spacer.
The only way would be to trim the hub to get the desired height.
This caused another issue, the Noath kit comes with a tapered bolt which is great for a direct bot on kit but if I had to trim the hub the bolt would no longer sit correctly in the tapper.
So I decided to drill the hub out to M14, and use an M14 rose joint instead.
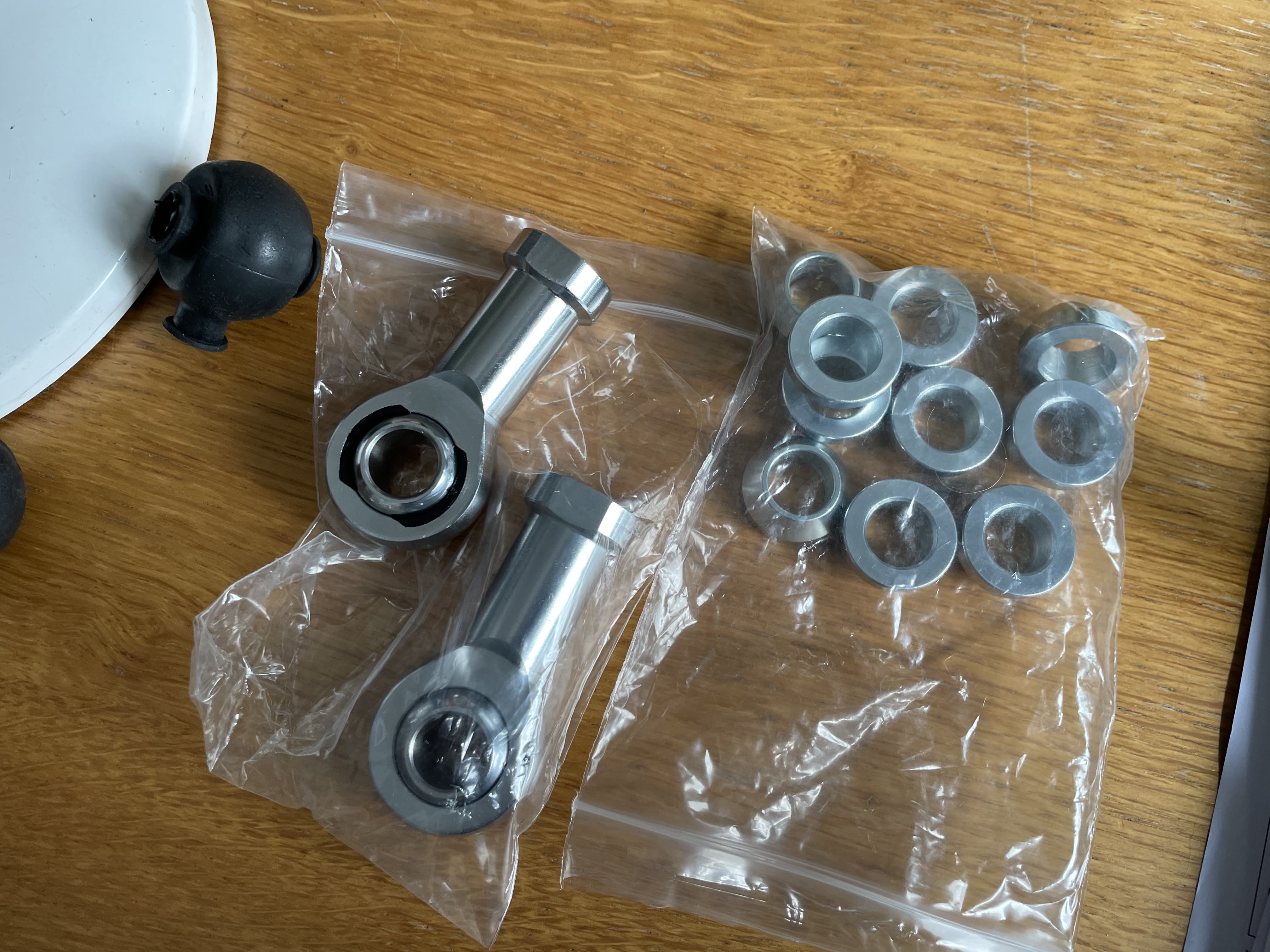
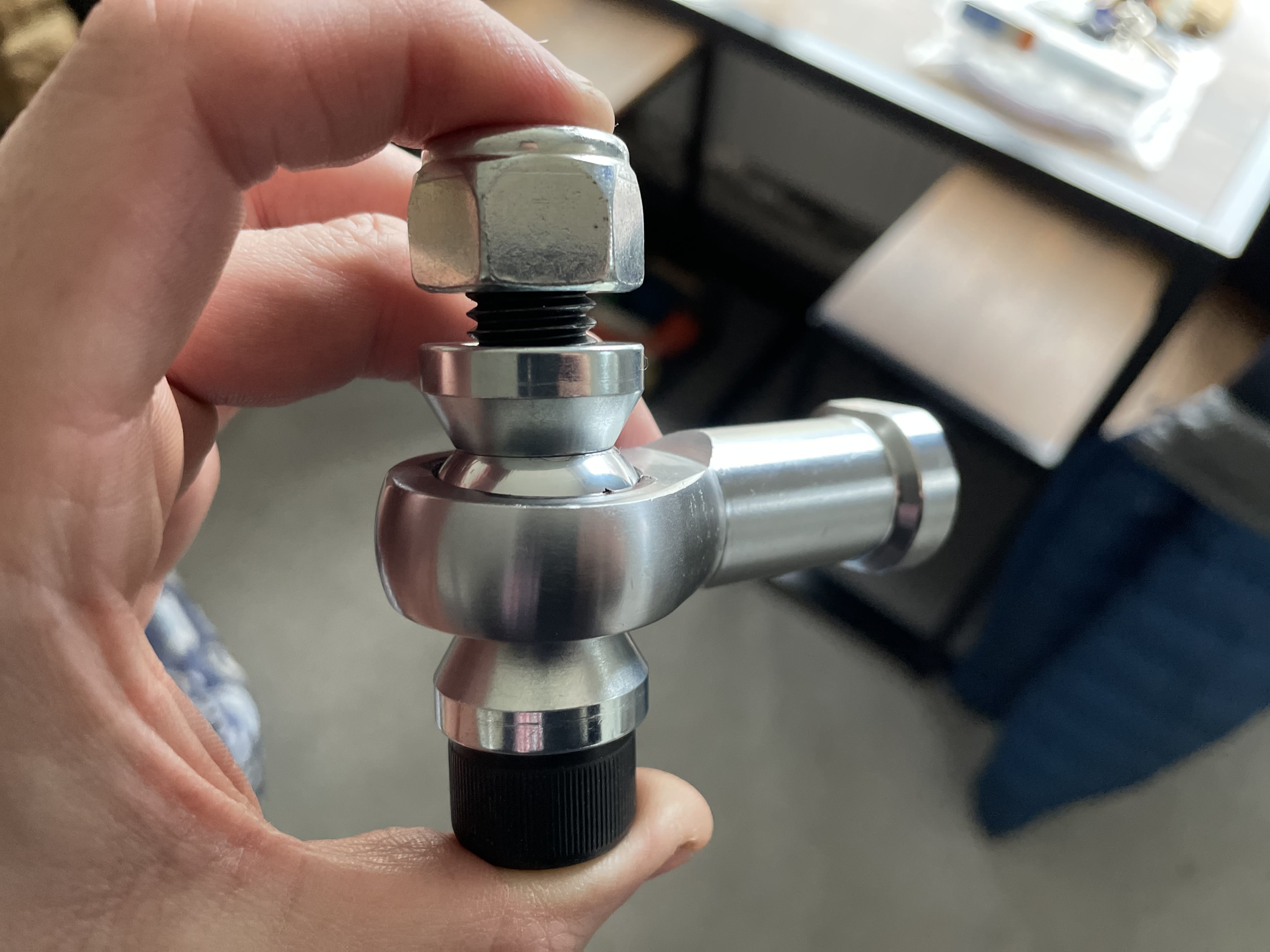
These were from McGill Motorsport, ordered on Friday afternoon, arrived Saturday!
I ordered their highest quality joints, misalignment spacers and rubber boots, costing £45.
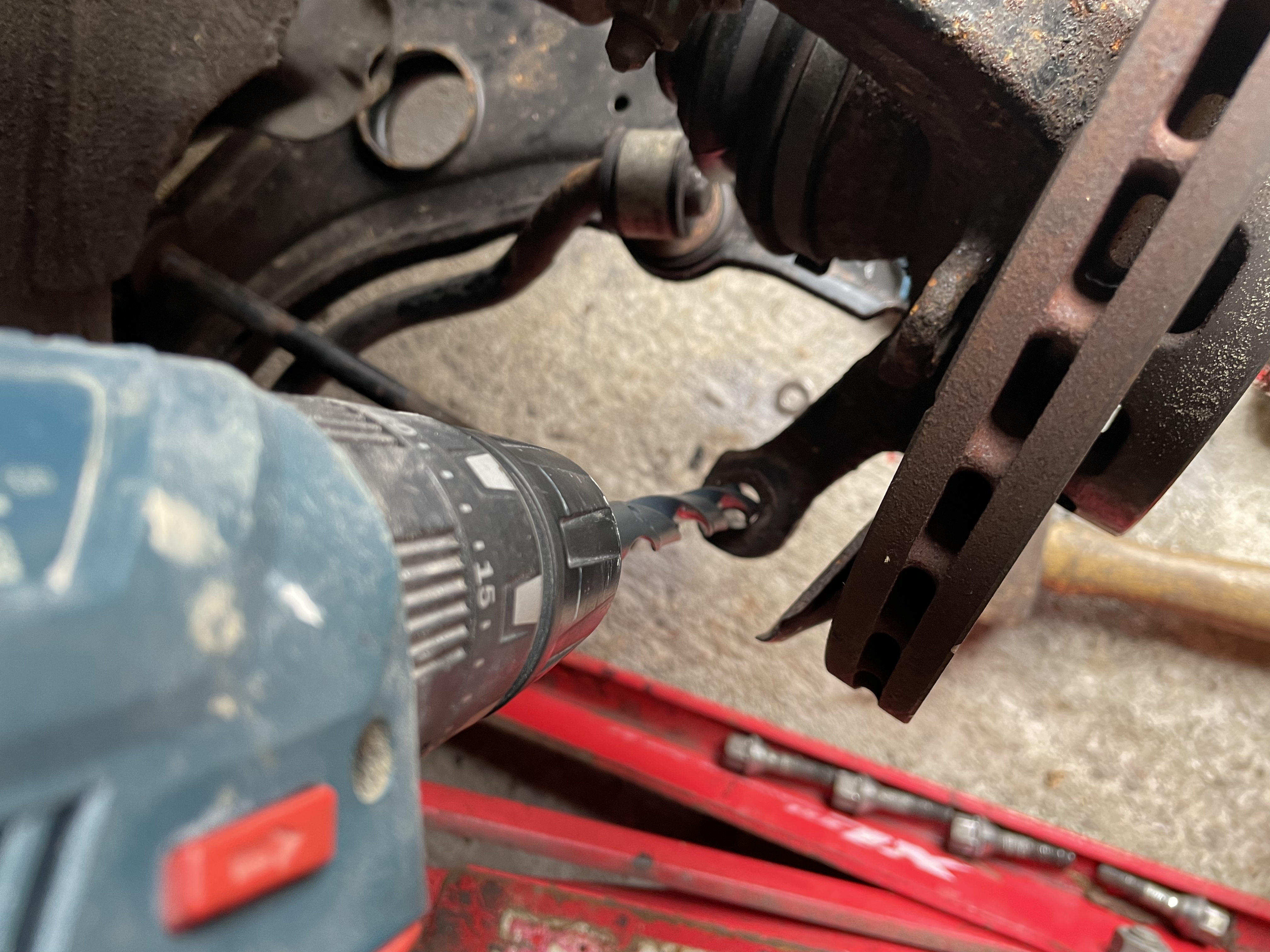
With the hub drilled out, I took 6mm off the hubs. The material I’ve taken off the bottom I’ll add back on the top to retain the strength in the arm, I’m just waiting for the steel to arrive.
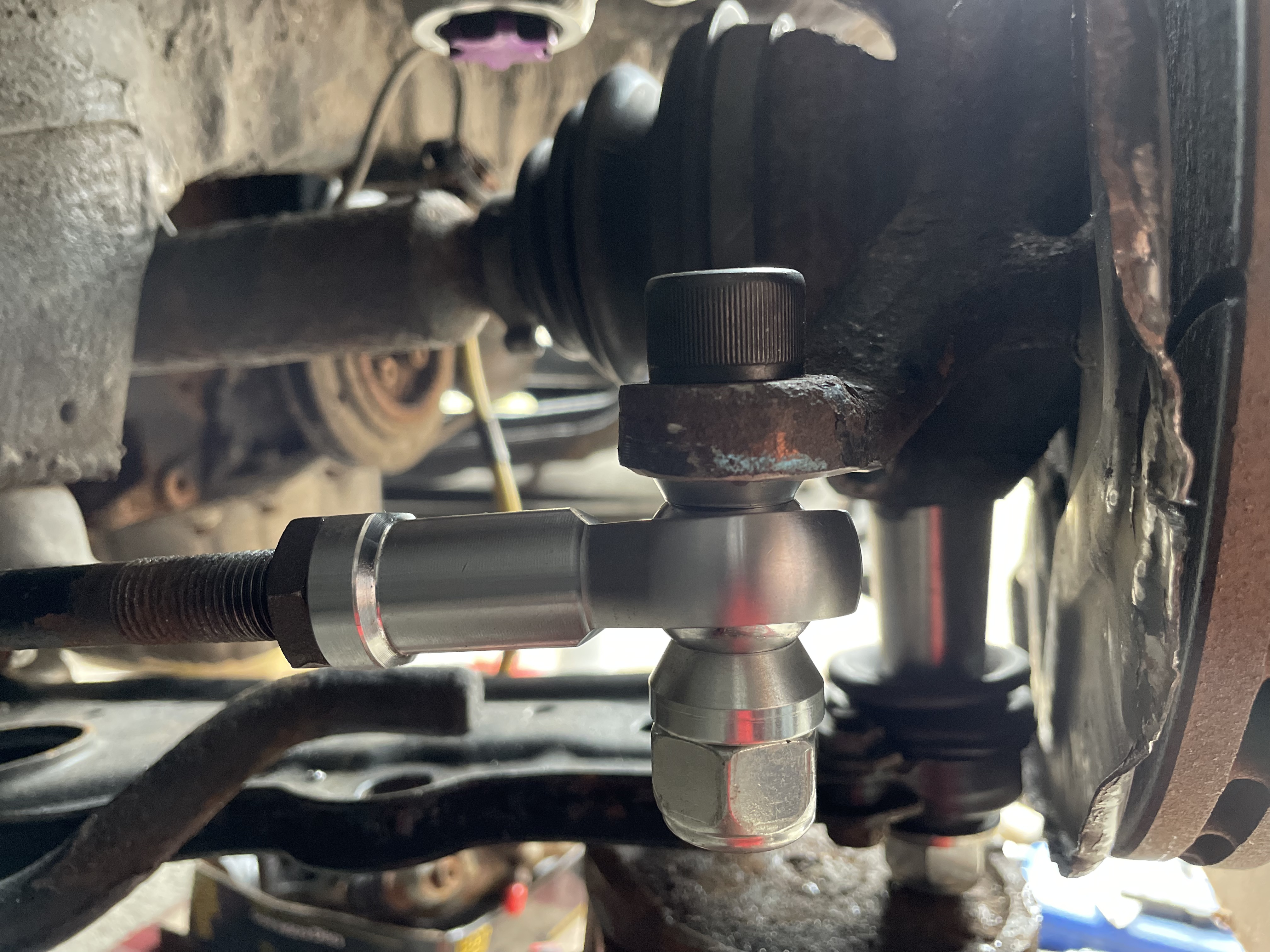
After the material was taken off and cleaned up, I cut one of the misalignment spacers down to 4mm and assembled.
I checked the articulation of the joint and there was still plenty of room and no binding in the joint.
I then plotted another graph:
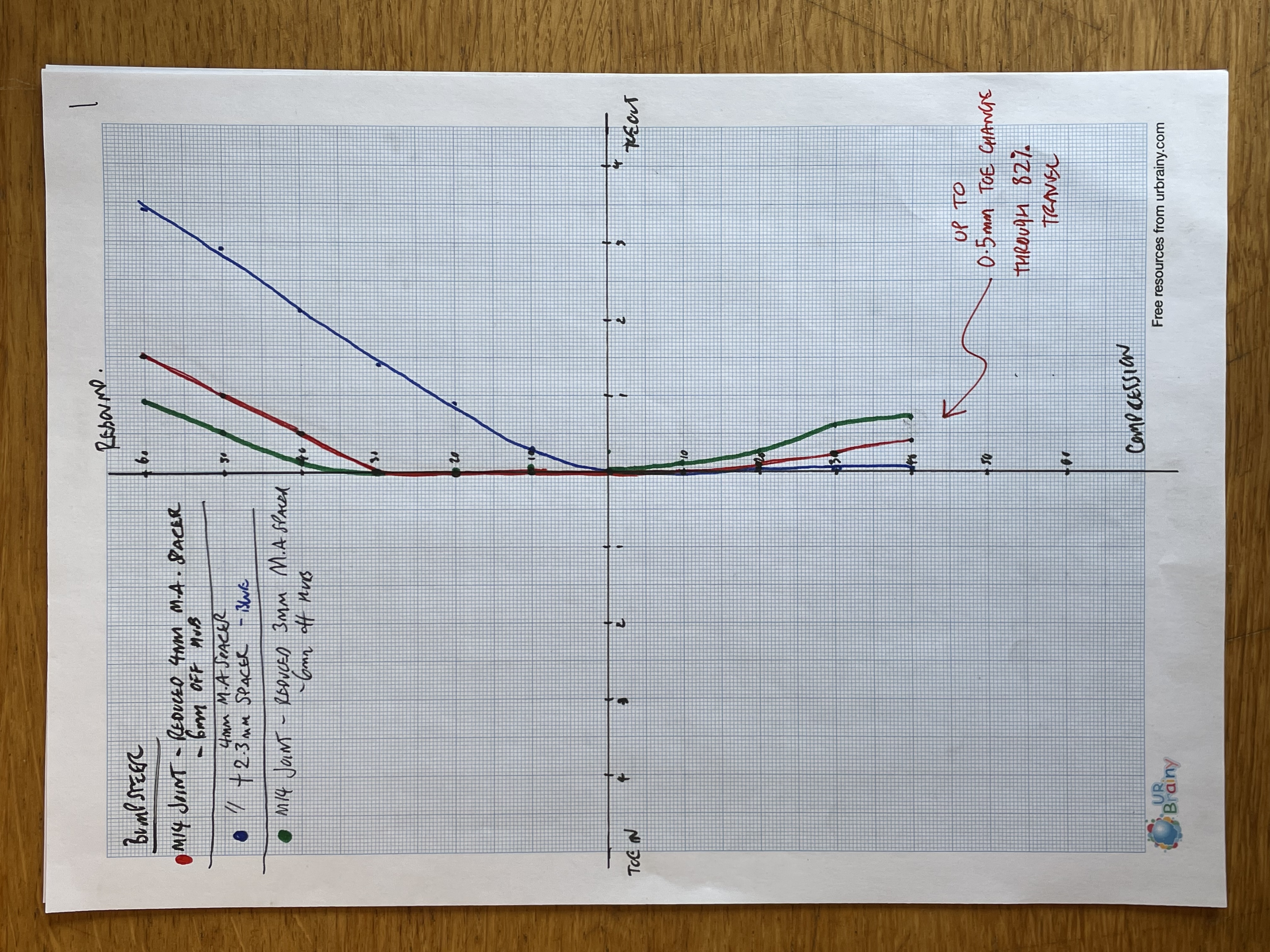
The above results I was absolutely chuffed with!
Red line is: Modified hub with M14 Joint, 4mm misalignment spacer
Blue line is: Modified hub with M14 Joint, 4mm misalignment spacer and 2.3mm washer
Green line is: Modified hub with M14 Joint, 3mm misalignment spacer
Looking at the data, the red line seems best for me, although green looks best on rebound, Red has the most usable area in zero bump, with up to 0.5mm of toe change over 82% of suspension travel.
The reason the graph arcs to toe out at the extreme ends of travel is because the track rod is effectively too long, the solution is either a wider rack, or fit rack spacers.
That will be version 2 of this project and for now I couldn’t be happier!

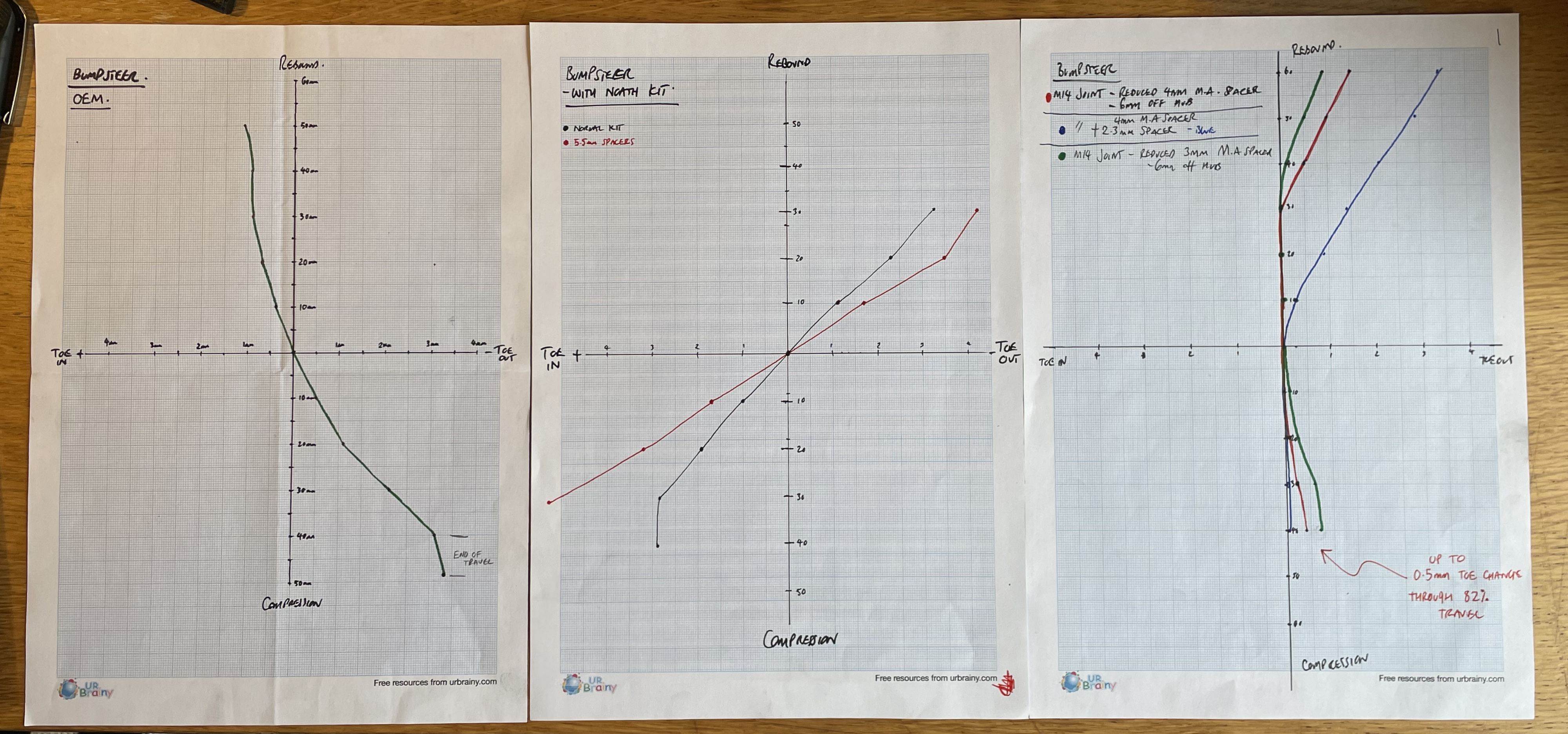
For those wondering I did some back to back test, and each data point was accurate to within 0.1-0.2mm,
I’ll settle for that with a DIY setup at a fraction of the cost!
Now I've just got to repeat on the other side.